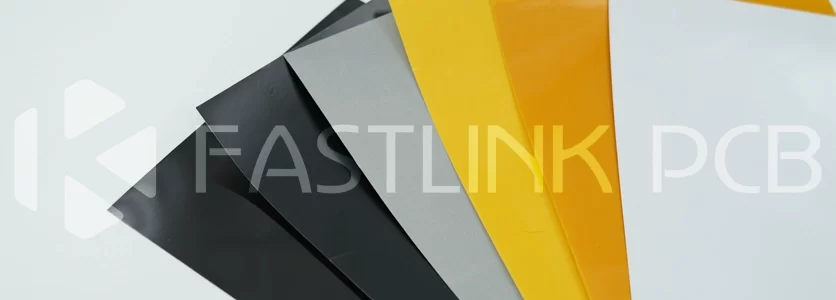
- On November 8, 2024
- In blog
9 Key Factors Affecting PCB Thickness
Thickness is a key parameter in the design and manufacture of PCB, affecting the performance and suitability of the PCB. So, how to determine the appropriate PCB thickness? In fact, the thickness of the PCB is not set in stone, it is affected by a variety of factor. Different design need, working environment and manufacturing requirement all have different impact on PCB thickness. Understanding these factor can help designers make better decisions. Next, we’ll look at 9 key factors that affect PCB thickness.
1.Thickness of the Substrate
Substrate are usually made of materials such as FR-4, PI, aluminium or ceramics, which provide the most basic structure for the PCB, and therefore have arguably the greatest influence of all factors on the thickness of the PCB. The thickness of the substrate can vary depending on the specific application. For example, in heavy-duty equipment that is subjected to high mechanical stress, choosing a thicker substrate (closer to 0.125 inches) enhance the robustness of the structure, while in space constrained smartphone, a thinner substrate (approximately 0.031 to 0.04 inches) is a better choice.
In addition thinner substrate are typically lighter and more flexible, but are more brittle and prone to fracture. Therefore, applications that do not require flexibility should choose a slightly thicker substrate to ensure adequate mechanical support. Flexible PCB, on the other hand, must use thinner substrate to achieve flexibility.
The following are some commonly used substrate material for Fastlink and the corresponding thickness data, which can provide you with reference.
Specification | Thicknesses(mm) | Plate thickness tolerance(mm) | Copper foil thickness | TG | Dielectric constant |
FR-4 | 0.2-7.0 | ±10% | 1/3oz,Hoz-6oz | 130,170 | 4.3-4.9 |
4350 | 0.5,0.8,1.0,1.6 | ±10% | Hoz,1oz | — | 3.48±0.05 |
4003 | 0.5,0.8,1.0,1.6 | ±10% | Hoz,1oz | — | 3.38±0.05 |
5880 | 0.5,0.8,1.0,1.6 | ±10% | Hoz,1oz | — | 2.20±0.02 |
5870 | 0.5,0.8,1.0,1.6 | ±10% | Hoz,1oz | — | 2.33±0.02 |
polyimide(VT-901) | 0.8,1.0,1.2,1.6,2.0 | ±10% | Hoz,1oz | 250 | 3.9-4.2 |
Aluminium substrate | 0.8,1.0,1.2,1.6,3.0 | ±10% | Hoz,1oz,2oz | — | — |
PTFE | 0.25-5.0 | ±10% | Hoz,1oz,2oz | — | 2.55-2.65 |
PCL | 0.1,0.2 | ±10% | 1/3oz,Hoz,1oz | ≥90 | — |
CCL | 0.3-3.0 | ±10% | 1/3oz,Hoz,1oz,2oz | 130,170 | — |
Arlon | 0.8,1.0,1.2,1.6,2.0,2.5 | ±0.13 | 1/3oz,Hoz,1oz | — | — |
2.Copper Thickness
The copper thickness of the PCB also has a great impact on the overall thickness of the PCB. In general, the thicker the copper layer, the greater the advantage of the board in carrying high current and withstanding heat. Standard copper thickness range from 1.4 to 2.8 mils (1 to 2 oz). When the copper thickness of a PCB exceeds 3 oz, it is often referred to as a heavy copper PCB. Heavy copper PCB are mainly used in application scenarios that require high currents and high heat dissipation performance, such as power supply modules, automotive electronics, and industrial controls.
Depending on the current carried by the board, we can choose the copper thickness we want. However, the thicker the copper, the thickness and cost of the PCB will increase accordingly. Moreover, due to etching limitations, the copper alignment width of thick copper PCBs should be greater than 6mil, so thick copper PCBs cannot support high-density alignment design.
3.Thickness of Solder Mask
The solder mask is a protective layer that cover the surface of the copper trace, and it is relatively thin, so it has less impact on the overall thickness of the PCB, but it should not be ignored. According to the IPC-SM-840 standard, the thickness of the solder mask should be 0.8 mils (about 20 microns) or more to ensure adequate protection. A thicker solder mask can more effectively protect copper alignments from environmental factors such as moisture and chemicals, enhancing the durability of the PCB.
However if the solder mask is too thick, it may lead to reduced pad gap, affecting the soldering accuracy of small component and increasing the risk of soldering defect. Therefore, the specific thickness should be weighed according to factor such as PCB application scenarios, component density and manufacturing process.
4.Thickness of Prepreg
Prepreg is mainly used to provide insulation and bonding between two core boards or between a core board and a copper foil. It is a mixture of glass fibre and resin, commonly used resins are epoxy or partially cured polyimide. Depending on the resin content, prepregs can be categorised as high resin (HR), medium resin (MR) and standard resin (SR). The more resin, the higher the cost and the thickness of the prepreg will increase accordingly.
The thickness of the prepreg affect the electrical properties of the PCB, such as impedance and drilling quality, as well as the dielectric constant and coefficient of thermal expansion (CTE). Common prepreg thicknesses are:
Prepreg | 0.5oz copper, 30% signal layer | 0.5oz copper, 70% planar layer | 1oz copper, 30% signal layer | 1oz copper, 70% planar layer | 2oz copper, 30% signal layer | 2oz copper, 70% planar layer | Top/bottom copper layer | Non-conductor layer |
106 | 1.9 | 2.2 | 1.5 | 2 | 2 | 2.5 | 2.3 | 2.1 |
1080 | 2.6 | 2.8 | 2.1 | 2.6 | 2.1 | 3 | 3 | 2.7 |
2113 | 3.5 | 3.8 | 3 | 3.6 | 3.4 | 4.1 | 3.9 | 3.5 |
2116 | 4.7 | 4.9 | 4.2 | 4.8 | 4.6 | 5.3 | 5 | 4.6 |
7628 | 6.5 | 6.8 | 6 | 6.5 | 6 | 6.9 | 6.5 | 6.2 |
Thickness: mil, 1/1000 inch; Tolerance: ±10 per cent |
5.PCB Layers
As the number of layers of a PCB increase, this usually result in an increase in overall thickness. This is because for each additional conductive layer (usually copper), a corresponding insulating layer (e.g. prepreg) is required for isolation and bonding. As the number of layer increases, so do the thickness of the PCB. Therefore, design that require more layer are usually faced with an increase in board thickness. If the design do not require a multilayer structure and has stringent thickness requirement, then reducing the number of layer would be a better option.
However, the thickness of a PCB is not entirely determined by the number of layer, and manufacturer can try to maintain the overall thickness by using different thicknesses of dielectric material. Thus single and double-sided PCB can also be designed to be very thick, and multilayer PCB are able to be made as thin as possible. It should be noted that as the number of layers increases, this control effect diminishes and there is a lower limit to the thickness. Specific figures need to be confirmed according to the manufacturer’s process capability and customer requirements.
Multilayer PCB have the advantage of being able to cater for complex circuits, providing feature such as high density interconnections, low EMI and high signal integrity. However, as the number of layers increases, the manufacturing process becomes more complex and costs rise, which may not be desirable in certain application scenarios. Therefore, designers need to make a thorough trade-off between circuit complexity, available physical space, thickness limitations, and cost when planning their PCBs.
6.Signal Type
Different signal characteristic will place different requirement on the material selection, number of layers and structural design of the PCB, thus affecting the overall thickness of the PCB.
High power signal: For PCB that transmit high power signals, thicker copper layer and wider alignment are required. For example, thicker copper foils and multilayer structure are often used in application such as power supply modules and high power amplifiers to ensure adequate current carrying capacity and heat dissipation.
High frequency signal: High frequency signal have stringent requirement for signal integrity and impedance control. In order to reduce signal loss and electromagnetic interference, thin high performance dielectric material and fine alignment design are often used. This can lead to a reduction in overall PCB thickness. In addition, microstrip or ribbon line structures are often used in high frequency PCB, which have specific requirements for layer spacing and dielectric thickness, also affecting the overall thickness of the PCB.
Mixed Signal: In mixed signal circuit that process both analogue and digital signal, effective signal isolation and shielding on the PCB is required. This is often achieved by adding grounding or shielding layer, which increase the number of layer and thickness of the PCB. In addition, layer spacing may need to be increased to reduce signal crosstalk, which also affect the overall thickness of the PCB.
7.Types of Holes
In the design and manufacture of PCB, different type of hole, such as through hole, blind hole, buried hole, and microvia, require different manufacturing processes and equipment, and also affect the final thickness of the PCB.
Through hole: Through hole run through the entire PCB layer, connecting the top and bottom layers, or all inner layers. For thicker PCB, the aspect ratio (the ratio of hole depth to hole diameter) of the drilled hole increase, which can lead to increased manufacturing difficulties. Typically, standard drilled hole have an aspect ratio of 7:1, but for thicker PCB, larger hole diameter may be required to meet manufacturing requirement.
Blind and Buried Hole: Blind holes connect an outer layer to one or more inner layer, while buried holes connect only between inner layer and do not penetrate the outer layer. These type of via are commonly used in HDI PCB that require precise interlayer alignment and control.
Microvia: Microvia are hole less than 0.15 mm in diameter, usually achieved by laser drilling techniques. They are used to connect layers of high-density wiring and are commonly found on HDI PCB. the use of microvia reduce the thickness of the PCB but require sophisticated manufacturing processe and equipment.
Limitation of drilling equipment: Manufacturer are limited in drilling holes by the thickness of the board and the diameter and depth capabilities of the drilling equipment (e.g. mechanical and laser drills). Thicker PCB may require larger hole diameters to meet the aspect ratio requirements of the equipment. Therefore, communication with the manufacturer is required during the design phase to determine the appropriate hole diameter and board thickness combination.
8.Application Environment
Application environment is also one of the important factor affecting PCB thickness. In high temperature or high humidity environment, PCB may experience problem such as material expansion, warping or delamination, and choosing a thicker PCB can improve its mechanical strength and thermal stability to ensure reliability. In application that require exposure to mechanical vibration, shock or stress, such as automotive and industrial equipment, thicker PCB can also provide greater rigidity and durability to prevent damage.
9.Cost and Time
The impact of cost and time on PCB thickness is mainly reflected in the design of custom thickness. Customized PCB thickness usually require manufacturer to make additional process adjustment and equipment configuration modification, a process that not only increase the time required for production, but also significantly increases manufacturing cost. Therefore, if your design does not have particularly stringent requirement for PCB thickness, and you wish to reduce cost and shorten production lead time, standard thickness PCB would be a more appropriate choice.
In the PCB industry, the earliest standard PCB thickness was 1.57 mm (0.062 inches). However, with the development of technology and the increasing complexity of circuit design, Fastlink can now provide you with multiple of standard PCB thickness option, including 0.78 mm (0.031 inches), 2.36 mm (93 mils), and 3.17 mm (125 mils), to meet the need of different application.
Wrapping Up
These are the nine key factor that affect PCB thickness. By gaining a deeper understanding and analysing these factor, designer can take better control of their PCB thickness choices. In practice, maintaining communication with the manufacturer about viable thickness options will also further optimise your design process. We hope that this article will provide you with a valuable reference for choosing the right PCB thickness and help your product stand out in the market.