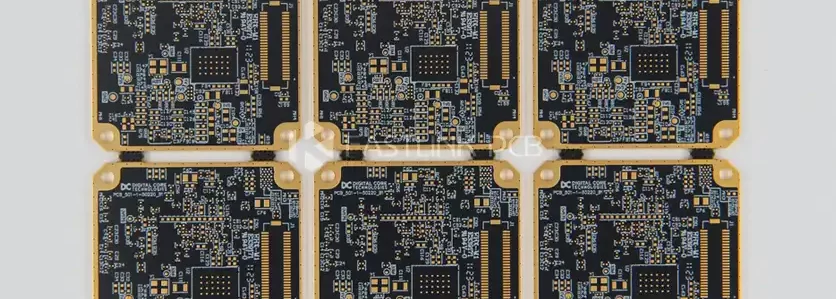
- On January 17, 2025
- In blog
Exploring Common Problems in PCB Engineering Review
In the PCB industry, the successful delivery of every order is dependent on a rigorous engineering audit. You may ask: Why is engineering audit so important? This is because a large number of practice has proved that an incomplete or inaccurate order information, often lead to production interruptions, repeated communication, delivery delays and a series of problems. Next, I will be based on the PCB manufacturing process to introduce you to the PCB audit order in the notes.
PCB Drilling Review Order Considerations
1.Drilling Form
- Ensure that a complete drill program and drill chart is provided.
- Drill markings in the outline drawing should be clearly labeled with size and properties.
- Drill size, number of vias, and attribute information must be consistent in the drill sheet.
2.Special Drilling Requirements
- If there are press fit hole, precision hole under 1 mm, or special process holes (e.g. outer layer sinking RING) please clearly indicate them in the data.
- If the distance from the edge of the hole to the edge of the board is less than 10 mils, please confirm with us in advance.
3.Through-hole Design Specifications
- The process tolerance of PTH holes is±3mil, please inform us in advance for special requirements.
- If half-hole design is required for PTH holes, please mark it clearly in the data.
- NPTH to PTH 8-hole design may have copper wire residue, please confirm in advance.
4.Important Parameter Control
- The minimum distance between the upper and outer coarse copper paths of the PAD around the NPTH or the distance from the copper is recommended to be not less than 5 mils.
- Special attention should be paid to the positioning of VIA HOLE in the BGA area.
- Gerber should have at least three apertures (1.5~5mm) between NP or PTH as the gong board positioning holes (try to choose NP holes).
5.Special Hole Shape
- For special process requirement such as countersunk holes, flared holes, please provide clear size specifications.
- 6.5mm NP round hole or 6.5×6.5mm square hole, it is recommended to control the tolerance of ±0.1mm.
- If the square hole design has inner R angle requirement, please specify in advance, because the minimum drilling pin of slot hole is 0.5mm, so the inner angle of Jianyi should be more than 0.5mm.
PCB Inner Layer Review Order Considerations
1.Structure and Material Design
- Make sure that the naming and ordering of layer in the Gerber file is consistent with the stacking table.
- The choice of substrate for the inner layer (e.g. H/1, 1/H, 1/2, 2/2, 3/3.) should be labeled.
- Clearly labeled cut-off line for area with different copper foil thicknesses.
2.Empty Copper Treatment and Copper Surface Design
- It is recommended to add cu bar or PAD in the inner and outer empty copper areas to prevent wrinkles of copper foil, uneven plating of the outer layer, thin lines, etc.
- Ensure that the inner copper surface is ≥ 0.2mm from the drilling edge in the design, and the specific distance can be adjusted according to the thickness of the PCB.
- The retention or removal of independent PADs should be determined according to SPEC or actual requirements.
3.Minimum Distance From Inner Drilled Holes to Wires
- 4/6/8-layer PCB: not less than 7mil
- 10-layer PCB: not less than 8 mils
4.Special Process Considerations
- For all-black or all-white inner layer, please specify whether it is made of all-substrate or all-copper (copper side of drilling sleeve).
- The copper side of the drilling sleeve should be calculated and the impact on the impedance should be evaluated. If there is a big difference between the two sides of the copper residue of the inner layer, it will affect the impedance. Especially for the outer layer.
- Special attention should be paid to the CAM calculation of the inner layer, and the impedance should be considered when the difference between the residual copper of the outer layer is more than 0.2mil. For example, if PP1-2 is 3.73mil and PP3-4 is 3.43mil in a 4-layer board, the impedance should be calculated separately and the average value of PP should not be used.
PCB Plating Review Order Considerations
1.Basic Requirements for Face Copper Hole Copper
- The most commonly used copper foil thickness is 0.5 ounces (oz)
- If your product needs to meet IPC standards:
IPC Class 1&2 Requirements: Copper thickness cannot be less than 1.4mil
IPC Class 3 requirements: copper thickness must not be less than 1.6mil.
2.Finished Copper Thickness
When you need 2 ounces of copper thickness, we will control it within the range of 0.2mil up and down. Especially for tin spraying boards this precision control is especially important.
3.Choice of Base Copper Design With Different Surface Copper
According to your actual needs, we provide the following options:
- When the finished copper requires Min2.4mil, the base copper is designed with 1oz.
- When the copper finish requirement is Min2.5mil, double-sided plate material number. Usually under 2OZ, need to confirm with the process of pressurization and copper reduction process.
- When the finished copper is 2.6mil<Requirement<3.2mil, the base copper will be designed with 1.3oz (line width compensation is the same as 2oz).
- When the copper completion requirement is Min3.2mil, the base copper is designed as 2oz.
- When the copper completion requirement is Min1.8mil, the base copper is designed with 0.5oz.
- When the finished copper is required to be Min1.9mil, please ask the engineering to confirm the design method with the process.
- When the finished copper is required to be Min2.0 mil, the base copper is designed with 1oz + copper reduction, and the specification after copper reduction is 0.8~1.2 mil.
4.Board Edge Copper Plating
If you need to do plating on the edge of the board, please note that the copper layer may be slightly shifted after plating, it is recommended to reserve 2mil margin in the design.
PCB Outer Layer Review Order Considerations
1.Line Width and Pitch Requirements
- Minimum line width and line spacing should meet the 3mil/3mil process requirements.
- The spacing between the connecting lines of BGA pads and their surroundings should be ≥3mil.
2.Drilling Distance
- The distance from PTH/NPTH holes to the surrounding copper wires should be ≥8 mil. if the distance is insufficient, please optimize the design to ensure process stability.
- The distance from the hole to the board edge should be ≥10 mil. if insufficient, it may lead to the risk of exposed copper or broken holes and need to be adjusted.
3.Copper Surface Design Requirements
- Is there any outer layer grid-like in Gerber? Grid <8*8mil needs to be confirmed to fill in the production.
- It is better to add cu bar or PAD to the outer empty copper area to prevent wrinkles, uneven plating of the outer layer, fine lines, etc. If not, PAD needs to be compensated for. Special attention should be paid to the board corner optical point should be enlarged.
4.Surface Treatment and Pad Design
- Design all other surface treatment boards except OSP, gold plating, electro-gold and tin spraying, such as: immersion silver, immersion tin, gold finger/immersion gold + OSP, gold plating + immersion silver, etc., need to confirm that the addition of teardrops, in order to improve the Giovanni effect of the open-circuit problem.
- Ensure that the distance between the pads and the surrounding wires is large enough to prevent soldermask from completely covering the pads and avoiding soldering short-circuit problems.
PCB Soldermask Review Order Considerations
1.Solderproof Layer Inspection
- Soldermask is consistent. If there is any inconsistency in the solder mask window or any conflict between the solder mask and the pad please mark it clearly. Confirm with us if necessary to avoid subsequent soldering problems.
- Match the size of the anti-solder window with the size of the pad to ensure that the anti-solder window of the PAD/SMD is properly designed. If the solder window on the pad is smaller than 12mil of the PAD size, it is recommended to optimize the window design. If not, please contact us for review.
- If there is a small window, please check if it can be reasonably enlarged. It is recommended to adjust the anti-solder width to ≥8mil to prevent the problem of poor exposure.
2.Ink Issues
- Pre-design optimization: Please make sure that the pad and copper surface spacing in the design can still meet the requirements for soldermask coverage and inking after the enlargement compensation. Especially for high-density design, it is recommended to reserve more spacing margin.
- Communication in advance: If the design involve high-precision or special color soldermask, please contact us in advance to confirm the process capability to avoid the problem of insufficient inking due to the small pitch.
- Color Selection: Green soldermask is usually the most stable choice for smaller pitch designs. If other colors are chosen (e.g. white, black or red) special attention need to be paid to the higher minimum pitch requirement.
3.Hole Plugging Issues
VIA hole and solder-proof design
If you have a VIA hole design with VIA touch solder-proofing (including the case of touch solder-proofing after VIA compensation), we recommend handling it in the following way:
D+2 (aperture plus 2 mils) for solder-proof windowing;
D+4 (aperture plus 4mil) for solder-proof overlay.
It is also necessary to confirm, whether the VIA holes are designed as half-plugged, full-plugged, or unplugged, in order to select the appropriate treatment method. If it is not clear, please specify or contact us for confirmation.
Confirmation of Plugging Requirements
If the plug hole requirement is not specified in your document, we will follow the standard process:
Single-sided solder-proof casement: Do half plug hole
Double-sided weld-resistant oil-covered: do full hole plugging
Double-sided anti-soldering openings: no hole plugging
If you have special requirements it is recommended to specify them in the document or contact us for confirmation.
Plugging hole and Gerber design consistency
If you have clear requirements for plug holes, we will check whether the Gerber design is consistent with your requirements. If there is a conflict between the design and the requirement, please indicate whether it can be adjusted directly to the Gerber; if not, we will ask for confirmation (EQ) before proceeding.
Large aperture VIA plug holes
If there are VIA holes ≥0.6mm in the design, please confirm whether or not hole plugging is required. If it is allowed not to plug the hole, please indicate whether it is acceptable for oil to enter the hole; if it is necessary to plug the hole, we recommend to reduce the hole diameter to 0.5mm before processing.
BGA area hole plugging
For BGA area design it is often necessary to plug the VIA holes. If the document does not explicitly state that the holes are not to be plugged, please check whether it is necessary to plug the holes.
Plugging direction
If the design requires hole plugging, please specify from which side the holes are to be plugged (e.g., top or bottom). We will mark this information in the manufacturing documentation (MI) to ensure that the process is accurate.
PCB Silkscreen Review Order Considerations
1.Text Color Confirmation
Please provide clear text color requirement or make sure it matches the description in the Gerber file. If there is any inconsistency in the color we will raise an engineering question to confirm with you.
2.Text Repetition and Reversal Issues
Please check whether the text in the Gerber file has any overlapping, reverse or wrong layout problems, especially pay attention to the labeling of the customer’s material number and version number. This information is very critical and it is recommended to focus on checking.
3.Text Line Between BGA Area and SMD
Check whether the text in the BGA area or near the SMD in the Gerber file need to be retained. If the text is not clear when the work piece is enlarged we will ask EQ to confirm how to deal with it.
4.Text Size and Line Width
Please make sure that the text size is not less than 24mil × 28mil and the text line width is not less than 4mil. Text smaller than this may be bold or blurred during the manufacturing process and shipment quality cannot be guaranteed. To ensure clarity, please confirm the text size in advance.
PCB V-cut Review Order Considerations
V-CUT is a common process used in PCB manufacturing for board separation. The following are some considerations:
1.Residual Thickness and Tolerance
The residual thickness of V-CUT should be ≥0.3mm with a tolerance of ±0.1mm. If the residual thickness of your design is less than 0.3mm, we recommend increasing the residual thickness to ensure the strength of the PCB. For thicker PCB it is recommended that the residual thickness not exceed 1/3 of the board thickness and preferably not more than 0.7mm.
2.Gerber Shrinkage and Angle Confirmation
Taking board thickness of 1.6mm and residual thickness of 1/3 as an example, the inner shrinkage corresponding to different V-CUT angles is as follows:
20 degrees: 13 mil;
30 degrees: shrinkage 16mil;
45 degrees: shrinkage 21mil;
60 degrees: 24 mil.
When the board thickness becomes thinner, the shrinkage can be reduced appropriately. It is recommended to check whether the inner shrinkage in your Gerber file is sufficient, if the inner shrinkage does not meet the requirements, we recommend to reduce the V-CUT angle, or to confirm whether it is allowed to break the hole and expose copper.
3.V-CUT TEST PAD
If there is a need for V-CUT test, we need to confirm whether it is allowed to add V-CUT TEST PAD in the board, if it is not clearly stated in SPEC, we will confirm with you through EQ whether it can be added.
4.V-CUT Jumper
If your design require a V-cut test pad, please make sure that the distance between the lower and upper part of the test pad is not less than 20mm. If the design is less than 20mm we recommend checking with EQ to see if it is permissible to change it to a corner punch or to increase the spacing by cutting a larger broken edge.
5.PNL V-CUT and Edge Distance Requirements
The distance from the V-CUT to the edge should be ≥15mm, if it is less than 15mm, we suggest using symmetrical layout and using V-CUT processing in the whole PNL to improve the stability and the effect of parting.
Final Thoughts
In this article, we explore together common issue that you may encounter during PCB engineering review, such as consideration for drilling, solder protection, typography and V-CUT. Our goal is to help you avoid potential risks during the design phase thus allowing for a smoother manufacturing process and ultimately delivering more reliable PCB product. We hope these contents can be helpful to you, if you encounter any problems in the actual project please feel free to contact FastlinkPCB!