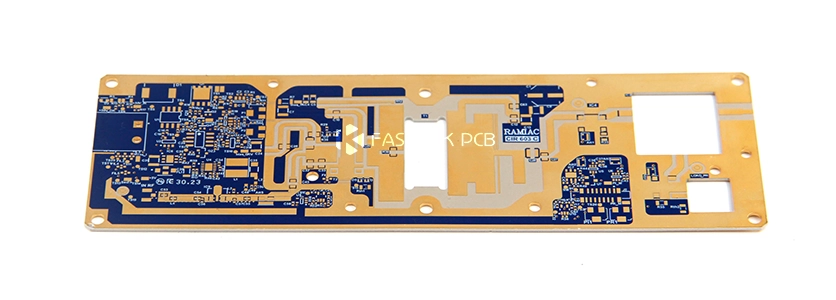
- On March 14, 2025
- In blog
High Frequency PCB Substrate | Isola, Rogers, Arlon, Taconic,
High-frequency PCB design is often jokingly called “black magic” by engineers, from the material selection stage is full of challenges. Currently on the market, Rogers, Isola, Taconic, Arlon and other big brands provide a variety of unique high-frequency substrates, but the complexity of the data on the parameter table often makes it difficult to choose. To make an informed choice, it is important to focus on 6 key indicators.
You can find these six key figures in the most data provided by the supplier: Dk, Df, water absorption, Tg, Td and copper foil surface roughness. They will affect the final properties of the HF PCB.
Dk and Df
Dk and Df are two of the most critical values in HF PCBs, where the Dk value determines the wavelength of the signal operating in the HF PCB and Df determines the signal attenuation. The following table shows the values of some common HF materials.
Brand | Substrate | DK(1GHZ) | DF(1GHZ) |
ISOLA
| FR408 | 3.77 | 0.011 |
FR408HR | 3.68 | 0.009 | |
IS680-345 | 3.45 | 0.0035 | |
ROGERS
| RO4350B | 3.48 | 0.0031 |
RO3003 | 3 | 0.0013 | |
RO4533 | 3.3 | 0.0025 | |
RO3730 | 3 | 0.0016 | |
ARLON
| TC350 | 3.5 | 0.002 |
AD300C | 2.97 | 0.002 | |
CLTE-AT | 3 | 0.0013 | |
Multiclad | 3.7 | 0.004 | |
TACONIC
| RF35A2 | 3.5 | 0.0011 |
TLY-5 | 2.2 | 0.0009 | |
TSM-30 | 3 | 0.0015 | |
TLX-8 | 2.45 | 0.0015 | |
RF35 | 3.5 | 0.0018 | |
TLC-30 | 3 | 0.028 |
High frequency design goals correspond to the selection:
- Long interconnections and risk of excessive loss: select materials with low Df.
- Small RF circuits: Select materials with high Dk values (shorter wavelengths).
The larger the Dk value → the shorter the signal wavelength → suitable for miniaturization.
(Note: Dk value does not affect the loss, but only determines the wavelength.)
It is also important to note that most high frequency materials need to have a consistent Dk value. This consistency is not only across a board, but also from batch to batch, over the temperature range in which the application may operate.
Water Absorption
Another key factor in maintaining the consistency of Dk values is the material’s water absorption. The lower the water absorption, the less the ambient humidity will interfere with the Dk, effectively maintaining the long-term stability of HF performance.
The following table compares the water absorption rates of the major common HF Substrates, with TACONIC performing better overall.
Brand | Substrate | Water Absorption |
ISOLA
| FR408 | 0.15% |
FR408HR | 0.06% | |
IS680-345 | 0.10% | |
ROGERS
| RO4350B | 0.06% |
RO3003 | <0.1% | |
RO4533 | <0.02% | |
RO3730 | 0.04% | |
ARLON
| TC350 | 0.05% |
AD300C | 0.06% | |
CLTE-AT | 0.03% | |
Multiclad | 0.10% | |
TACONIC
| RF35A2 | 0.02% |
TLY-5 | <0.02% | |
TSM-30 | 0.03% | |
TLX-8 | <0.02% | |
RF35 | 0.03% | |
TLC-30 | <0.02% |
Tg and Td
These two values relate to the thermal performance and mechanical strength of HF PCBs. Serious consideration is needed if your PCB needs to be used in high reliability equipment such as high frequency aerospace equipment.
1. Glass transition temperature (Tg)
- High temperature stability: The higher the Tg, the less likely the material will soften and deform under soldering or high temperature environments, safeguarding the precision of the circuit structure.
- Mechanical strength: high Tg material in the temperature cycle can reduce the thermal stress caused by the substrate micro-cracks
3. Thermal decomposition temperature (Td)
- Extreme temperature tolerance: The higher the Td, the less likely the material will carbonize and decompose under overload/high-temperature operating conditions.
- Long-term reliability: Higher Td materials reduce the risk of dielectric property (Dk/Df) drift caused by high temperature aging.
The difference between Td and Tg is that when a material reaches or exceeds its Td, the change in properties is irreversible. When the material is cooled down to its Tg value, the properties can be restored to their original state.
Copper Foil Roughness
Z-axis RMS roughness of copper foil (typical value 0.3-3 μm), the smaller the value the smoother the surface. As high-frequency signals (>1 GHz) are transmitted in the conductor surface layer, the rough surface enhances the skin effect, resulting in:
- Increased impedance deviation (±5% or more)
- Increased conductor losses (15-20% for every 0.5 µm increase in roughness).
Therefore, it is best to use rolled annealed copper or thin, coarse copper with the lowest possible loss for high frequency materials.
There is also a certain amount of roughness loss due to electroplated materials that also introduce rough interfaces in the copper layer. If you are running above 2.4 GHz Wifi or have long interconnects, then it is recommended that Organic Solderability Preservation (OSP) and Immersion Silver (ImAg) are required. Both of these finishes have little to no additional loss.
Material Cost
In addition to performance, the cost of the HF material is also a key factor influencing the choice. Substrate prices of different brands vary significantly, usually showing a positive correlation between “performance and price”:
- High-end brands (Rogers, Arlon): price indexes as high as 100-150 (100 based on FR4)
- Mid-range brands (Isola, Taconic): price index of about 60-90
- China-made alternatives (SYST, ITEQ): price index down to 40-70
Final Thought
At FastlinkPCB, we typically keep HF laminates from Isola, Rogers, Arlon, Taconic, Panasonic, SYST and 12 other leading brands in stock to minimize the cost of procurement time. However, it is always a good idea to contact FastlinkPCB in advance to ensure that we have the specific HF material you need for your new project. If you are still unsure of the HF PCB material you need, feel free to contact us as well. Our engineering team can give you some professional advice.