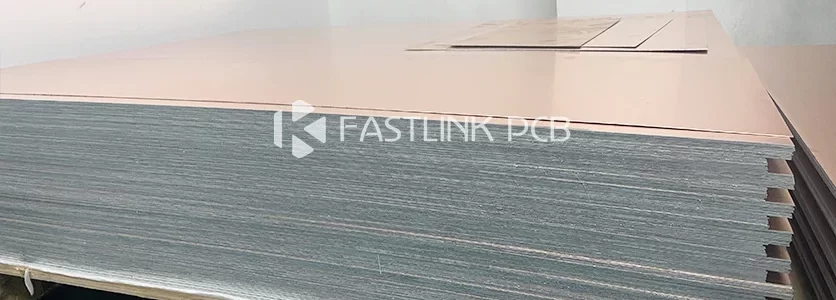
- On September 5, 2024
- In blog
How to Choose Between Aluminum PCBs and Copper PCBs?
In the era of ever-increasing miniaturization and escalating power density of electronic devices, the thermal dissipation capabilities of PCB substrates have emerged as a pivotal factor influencing product reliability. Renowned for lightweight nature and ease of processing, aluminum substrates stand out; while copper substrates boast remarkable electrical conductivity and thermal conductivity. This blog delves into their advantages, disadvantages, and applications to help you provide better material selection recommendations before designing your products.
What Are Aluminum PCBs and Copper PCBs?
Although Aluminum PCBs and Copper PCBs are belong to MCPCB (metal core PCB), they have different characteristic and applications.
Prior to comprehending their definitions, you need to have a foundational understanding of what substrate is. Substrate is the base material that forms the foundation of a PCB commonly constructed with FR4, a fiberglass-reinforced epoxy resin material, or other composite materials manufactured to provide mechanical support and electrical insulation also serving as a platform for copper foils.
Copper PCB can also be referred to as copper core PCB or copper based PCB, it makes use of a copper base as a layer for dissipating heat, this particular kind of PCB is designed for using scenarios that require effective thermal control guaranteeing the best possible dispersion of heat while in use.
The aluminum PCB consists of three layers: the circuit layer (made of copper foil), the dielectric/insulating layer, and the aluminum base layer. This aluminum core provides good thermal conductivity, allows more efficient heat dissipation. Aluminum PCBs are also known as aluminum clad, aluminum base, IMS (insulated metal substrate), and thermally conductive PCBs.
Applications of Aluminum PCBs and Copper PCBs
Copper based PCB is suitable for applications in consumer electronics, such as smartphones and tablets, as well as in industrial equipment, automotive electronics and telecommunications device, also ideal for high frequency applications, like RF and microwave devices, and power electronics.
Copper PCBs Application | Specific Devices |
Audio Equipment | Input amplifiers, output amplifiers, balanced amplifiers, audio amplifiers, preamplifiers, power amplifiers |
Power Supplies | Series regulators, switching regulators, DC-AC converters |
Telecommunication Equipment | High-frequency amplifiers, filter circuits, transmitting circuits |
Office Automation | Printer drivers, large electronic display substrates, thermal printheads |
Automotive | Ignition systems, power regulators, AC inverters, power controllers, light control systems |
Computers | CPU boards, floppy disk drives, power supply units |
Power Modules | Converters, solid-state relays, rectifiers |
High-frequency applications | RF and microwave devices |
Aluminum based PCBs are particularly suitable for products that require excellent thermal management and light weight, are commonly used in high power LED, automotive component, power supplies and industrial machinery.
Aluminum PCBs Application | Specific Devices |
High-Power LED Lighting Systems | LED drivers, power supplies, heat sinks |
Automotive Components | Battery management systems, inverters, controllers |
Power Supplies | High-power rectifiers, DC-DC converters, AC-DC converters |
Industrial Machinery | Motor control units, power distribution boards, sensors |
Fastlink suggests you choose copper-based PCB for high-power and high-frequency applications where superior thermal and electrical properties are required. Aluminum-based PCBs are more suited to cost-sensitive applications with moderate heat generation, space-constrained and portable devices, environments with potential corrosion.
Appearance of Aluminum PCBs and Copper PCBs
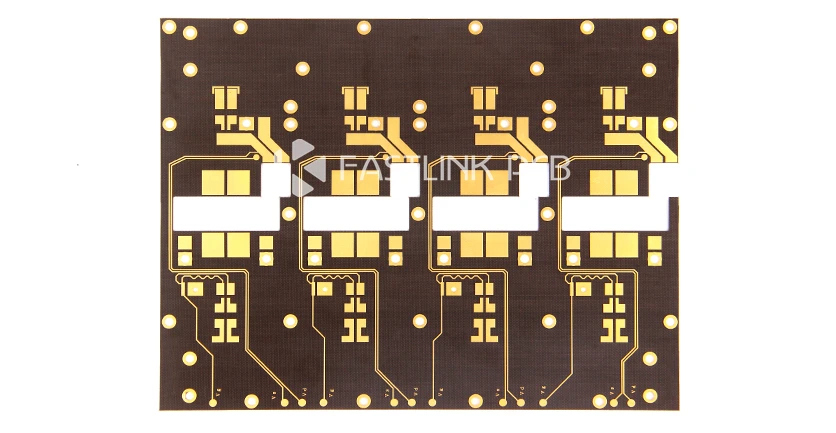
copper core pcb
You can tell aluminum and copper PCBs apart just by looking, aluminum PCBs are usually silver gray and really shiny, reflecting light well. On the other hand, copper PCBs have a yellowish color and have a relatively smooth texture.
Electrical performance Aluminum PCBs and Copper PCBs
The electrical conductivity of aluminum is 37.8 MS/m, inferior to copper. Specifically, in the design of aluminum-based PCBs, meticulous attention must be paid to the configuration of the electrical insulation layer to prevent circuit shorting or signal interference.
Conversely, the electrical conductivity of copper-based PCBs is exceptionally high as 59.6 MS/m, the superior electrical performance is ideally suited for applications involving high currents and voltages. Despite the necessity for an insulation layer similar to aluminum substrates, copper’s electrical performance typically remains unaffected to a significant degree.
Thermal performance Aluminum PCBs and Copper PCBs
Aluminum has thermal conductivity of 237 W/m-K, but copper blows it out of the water with 401 W/m-K, means copper PCBs are way more efficient at conducting heat and dissipating it, so they’re less prone to warping or corrosion over time compared to aluminum PCBs.
Weight Aluminum PCBs and Copper PCBs
The density of aluminum is 2.7 g/cm³, whereas copper possesses a higher density of 8.96 g/cm³. Consequently, aluminum is lighter than copper, leading to an overall reduced weight in aluminum-based PCBs, rendering aluminum based PCB ideal for lightweight designs.
Mechanical Strength Aluminum PCBs and Copper PCBs
Copper surpasses aluminum in terms of strength, hardness, and wear resistance, it is suitable for applications requiring high strength and durability. However, copper’s relatively heavier weight and higher cost present drawbacks in comparison, unsuitable for weight-sensitive applications.
Manufacturing Complexity of Aluminum PCBs and Copper PCBs
Manufacturing aluminum based PCBs is quite simple, it is a good option for single layer PCB and basic designs; whereas producing copper based PCBs comes with more difficulties especially when it comes to multi layer designs, but is great for applications needing intricate circuit designs.
Material Processing
Copper PCBs are more difficult to make than aluminum PCBs in terms with material. Aluminum boasts a low density coupled with superior machinability, is easier cutting and shaping of aluminum substrates. In contrast, copper is denser and harder and requires higher processing techniques to handle.
Fastlink employs laser cutting and drilling techniques to achieve better precision than machine drilling, making it the perfect choice for intricate copper substrate cutting and micro-hole processing. Laser cutting eliminates mechanical stress on materials and guarantees clean, burr-free, and smoothly finished cutting edge.
Lamination
The lamination process for aluminum PCB is relatively straightforward, primarily involving the integration of insulation layers with the aluminum substrate, dispensing with overly intricate techniques. In contrast, the lamination process for copper-based PCB, especially in multilayer designs, is more intricate. Fastlink adopts advanced lamination equipment and implements rigorous control over temperature, time and pressure to ensure effective adhesion between individual layers.
Mixed Stackup
The process of mixed stackup is commonly utilized in creating rigid PCBs by stacking different materials alongside FR4, layer by layer to achieve complex circuit designs and functional division across multiple layers. For instance, aluminum can be employed at places requiring heat dissipation of LEDs, while FR4 layer is incorporated in other regions to meet the mechanical strength and cost efficiency. The mixed stackup method harmoniously merges the strengths of various materials providing design flexibility and optimizing cost.
Routing
The routing of single layer aluminum PCB is relatively simple. Copper PCB, on the other hand, is suited for high density and complex circuit designs, encompassing multilayer PCB and high frequency applications. The superior electrical conductivity of copper enables it to support more intricate routing requirement.
While most copper PCB manufacturers can achieve a minimum trace width and spacing of 4/4 mil with vias as small as 8 mil (0.2 mm), industry leaders like Fastlink push the boundaries of technology. We offer a remarkable trace width and spacing capability of just 2.5/2.5 mil, along with laser-drilled vias down to 4 mil (0.1 mm).
Soldering
High-thermal Conductivity
Copper and aluminum have high thermal conductivity, heat tends to dissipate quickly during soldering, potentially leading to poor welding results. Fastlink tackles this by employing high-temperature welding techniques, backed by advanced welding equipment and rigorous process control standards.
Surface Oxidation
Copper and aluminum is prone to oxidize forming a layer of aluminum oxide and copper oxide hindering the wettability of solder, resulting in soldering defects. Fastlink meticulously removes any oxide layers and uses special flux to ensure the soldering quality.
Solder selection
For aluminum based PCB, regular solders aren’t suitable, especially for low temperature soldering, as they might not wet the surface properly. So, to enhance the reliability of the soldering process, Fastlink opts for specific solders containing indium or zinc.
For copper based PCB, regular solders aren’t suitable because they are not wet and flow well at lower temperatures due to the copper’s high thermal conductivity, increasing the risk of cold or dry joints. To handle this, we utilize high melting point solders with superior wettability.
Soldering Temperature Control
Given the significant thermal capacity of copper and aluminum, precise temperature control during soldering is crucial. Excessive heat could damage components on the PCB, while insufficient heat may result in weak soldering. Fastlink carefully manages temperatures to strike the perfect balance ensuring robust joints.
Layer count
Single-layer structure is a better choice for aluminum PCB. Because aluminum base PCB typically comprises a tripartite configuration: a thermally conductive insulation layer, an aluminum substrate, and a copper circuitry layer, the simplistic structure lends itself ideally to single-layer circuit designs. Featuring remarkable heat dissipation capabilities, aluminum base plates are exceptionally suited for high-power-density applications such as LED lighting, power modules, and automotive electronics. These applications often necessitate a single-layer design to achieve efficient thermal management.
Multi-layer designs are suited for copper based PCB due to copper’s significantly superior thermal conductivity and high mechanical strength compared to aluminum. Fastlink boasts extensive experience and capabilities in manufacturing copper-based PCBs, with a maximum production capacity of 6 layers. In the industry, the number of layers in copper PCB typically does not exceed 6, this is because that multi-layered copper PCB can give rise to thermal management constraints and complicate the manufacturing process. And for applications such as LED lighting, where the primary requirement revolves around efficient heat dissipation rather than intricate circuit routing, the necessity for multiple layers of circuit design is generally not warranted.
Packaging
Given that aluminum and copper are prone to oxidation and corrosion in humid environments, with copper being particularly susceptible to the adverse effects of moisture, Fastlink typically employs vacuum packaging or moisture proof bags to hermetically seal these metallic PCB. And desiccants are placed inside the packaging to absorb any excess humidity.
Cost of Aluminum PCBs and Copper PCBs
In recent years, the market price for copper has hovered around the range of 7,000 to 10,000 per metric ton, the market price for aluminum has been approximately 1,500 to 2,500 per metric ton, the price of copper is generally about 3 to 5 times higher than that of aluminum. Plus the increased processing complexities associated with copper, the production of copper-based BCB tends to be significantly more expensive than aluminum PCB. So, we advise that aluminum PCB suit to applications requiring rapid production cycles and lower costs.
Why Choose Fastlink to Fabricate Aluminum PCBs and Copper PCBs?
Fastlink specializes in special materials PCB products. As a “specialized, refined, unique, and innovative” manufacturer, we provide rapid prototyping, mid-volume, and high volume manufacturing service tailored to meet your specific need. Check our capabilities as follows:
Specification | Capabilities |
Layer count | 1-6L |
Mixed stackup | FR-4+aluminum substrate FR-4+copper substrate |
Aluminum substrate | 3003, 5052, 6061 |
PCB thickness | aluminum substrate 0.6-5.0mm copper substrate 0.6-3.0mm |
Thickness tolerance | ≤1.0mm: +/-0.10mm, >1.0mm:+/-10%. |
Minimum pcb size | 500x1200mm |
Maximum copper thickness | 10oz |
Minimum trace width/space | 2.5/2.5mil |
Surface finish | LF HASL/LEAD HASL, ENIG, OSP |
Testing | X-Ray Testing, Functional Testing, AOI, Flying Probe Testing |
Certifications | ISO 9001, ISO 14001, UL, RoHS, ISO 13485, IATF 16949 |
Standards | IPC 2 or 3 |
Seasoned Engineers
Every metal material boasts its unique thermal conductivity and electrical conductivity, at Fastlink, we’ve got seasoned engineers who take into account these specific metal properties when designing copper and aluminum PCB.
Extensive Experiences
Fastlink’s precision lamination process guarantees a robust bond between the metal substrate and insulating layer, our manufacturing experience enables us to set pressure, time and temperature setting for various metals.