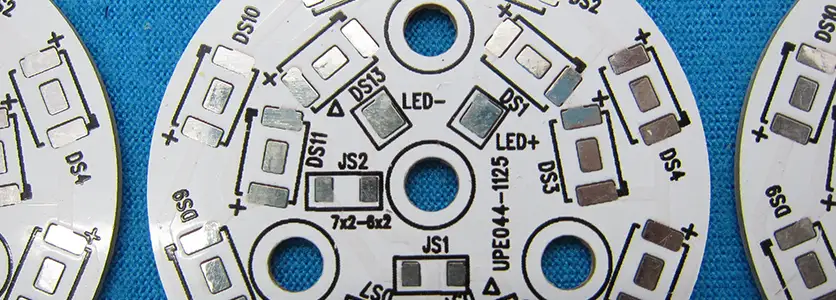
- On December 28, 2023
- In blog
The Role of Aluminum PCB Material in Electronics
Printed Circuit Boards (PCBs) are integral components in numerous electronic devices, ranging from simple LED lights to sophisticated scanners. These PCBs are produced from different materials to meet specific needs related to electrical conductivity, insulation, and durability. In contrast to conventional PCBs that often employ an FR-4 fiberglass base, aluminum PCBs utilize a metal substrate, mainly consisting of aluminum alloy. This distinction in material choice allows for varied performance characteristics suited to different electronic applications.
In this article, let’s find out what aluminum PCBs are and their role in the field of electronics.
What Is Aluminum PCB?
The primary advantage of using an aluminum PCB in manufacturing lies in its ability to effectively dissipate heat. Electronic devices often generate substantial heat, making efficient heat management crucial for maintaining stability and functionality.
An aluminum PCB incorporates an aluminum core followed by an FR4 layer. A key feature is the thermal clad layer, which serves to effectively disperse heat. This design focuses on providing a cooling mechanism for the device’s components, which, in turn, can improve the device’s overall performance.
The choice of an aluminum PCB is particularly beneficial for high-power devices that demand precise heat tolerance to prolong their operational lifespan. This makes aluminum PCBs a fitting choice for applications where managing intense heat is essential for maintaining device integrity and performance.
What Are the Benefits of Aluminum PCBs?
1. Eco-Friendly: Aluminum is non-toxic and recyclable, making it an environmentally friendly choice. Its integration into circuit boards conserves energy, further benefiting the environment.
2. Heat Dissipation: Ideal for high-end devices that generate substantial heat. Efficient and uniform heat dispersion helps cool devices quickly, extending lifespan and enhancing performance.
3. Durability: Combines flexibility with rigidity, offering greater durability than ceramic or fiberglass bases. This durability leads to an extended lifespan of the circuit board.
4. Manufacturing Efficiency: Easier to manufacture due to its balance of flexibility and strength. Reduced risk of breakage and damage during production and use.
5. Lightweight yet Strong: Adds resilience to devices without significantly increasing their weight. Lighter weight makes transportation and handling more cost-effective.
6. Cost-Effective: More affordable than copper and ceramic materials. Lower production costs compared to other metal-based PCBs in the market.
Applications of Aluminum PCB
Aluminum PCBs have good thermal performance, durability, and cost-effectiveness and are, therefore, widely used in various industries.
1. LED Lighting: One of the most common applications of aluminum PCBs is in LED lighting systems. The excellent heat dissipation of aluminum helps manage the high temperatures generated by LEDs, thus prolonging their life and enhancing their efficiency. This application ranges from residential and commercial lighting to specialized uses in automotive and street lighting.
2. Automotive Industry: In the automotive sector, aluminum PCBs are utilized in various components due to their ability to withstand vibrations and high temperatures. They are used in control systems, LED lighting, power regulators, and electronic control units (ECUs).
3. Computer Hardware: In computer systems, aluminum PCBs are used in power devices, motherboards, and graphic cards. They help in effective heat transfer, ensuring these components function within optimal temperature ranges.
4. Telecommunications: They are extensively used in telecommunications for equipment like high-frequency amplifiers and filtering appliances. Aluminum PCBs provide a stable and durable platform necessary for the reliable operation of communication devices.
5. Medical Equipment: In medical devices, especially those requiring high power and sterilization, aluminum PCBs are preferred. They are found in medical scanning technology, light equipment for surgeries, and monitoring devices.
6. Industrial Applications: In industrial settings, aluminum PCBs are used in power equipment, machinery controls, and robotic systems. Their durability and heat management capabilities are crucial in these high-demand environments.
7. Aerospace and Defense: The aerospace and defense sectors utilize aluminum PCBs in applications where reliability under extreme conditions is non-negotiable. This includes satellite equipment, control system components, and power converters.
8. Power Electronics: In power electronics, aluminum PCBs are essential for high-load applications like voltage regulators, converters, and switch-mode power supplies.
Aluminum PCBs in Electronics
● Longevity and Reliability: By effectively managing heat, Aluminum PCBs enhance the longevity and reliability of consumer electronics. This is particularly important in devices that are used continuously, like refrigerators and televisions.
● Energy Efficiency: Good thermal management also translates to better energy efficiency. Devices with well-managed heat dissipation consume less power, as they operate more efficiently and require less cooling.
● Compact and Lightweight Designs: Aluminum PCBs allow for more compact and lightweight designs in consumer electronics. This is particularly beneficial in portable devices where space and weight are critical factors.
Final Words
Aluminum PCBs are more cost-effective than other types of PCBs, such as copper, because they do not require any additional components or materials to manufacture. Fastlink is one of the best companies for manufacturing aluminum and other types of PCBs. We have been manufacturing these products for over a decade and have developed some outstanding technologies that allow us to produce these products at extremely low costs while still maintaining high quality standards. Therefore, if you are looking for an aluminum PCB manufacturer, please contact us!
Leave a comment