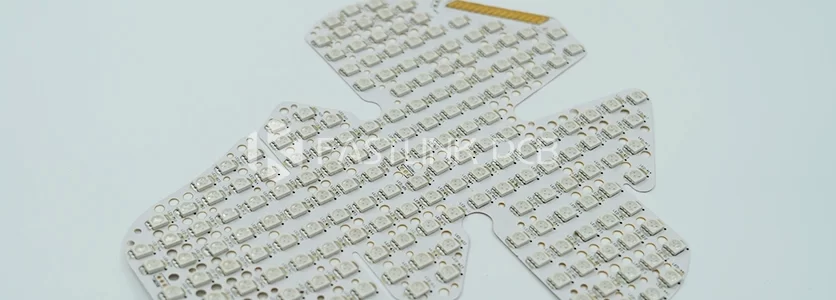
- On December 3, 2024
- In blog
What Do You Need to Know About LED PCBs
Light-emitting diodes (LEDs), an increasingly popular lighting technology, are being used in a wide range of industries, from gaming device and lighting system to home décor and industrial human-machine interfaces. As a solid-state lighting device, LED convert electricity into light through semiconductors, reducing energy consumption by up to 80% and extending service life by up to 25 times compared to traditional light bulb. In addition, LED also has a small size, environmental protection and many other advantage. In the next section, we will explore the different materials and types of LED PCBs, and help you better complete your LED PCB projects with some design considerations and assembly case studies.
Different Types of LED PCBs
Flexible LED PCBs
Flexible LED PCBs are crafted from either polyimide (PI) or polyethylene terephthalate (PET) materials offering flexibility and ideal for use, in LED strips or distinctive lighting creations.
Epoxy Resin LED PCB
Epoxy resin is also a common LED PCB material with low production costs. However, it is less durable than other materials and is typically used in budget-sensitive scenarios that require less strength.
FR-4 LED PCB
FR-4 is a common PCB substrate made of fiberglass and epoxy resin with good flame retardant properties. However, with a thermal conductivity of about 0.3W/m.K, it has limited heat transfer capability so it is usually better suited for require less thermal management LED application.
Ceramic LED PCB
Ceramic PCB have excellent thermal conductivity and electrical insulation, can dissipate heat quickly. Their durability makes them suitable for high power LED lamp used in high temperature, high intensity environment, such as industrial and automotive application.
Copper LED PCB
Copper-based LED PCB are a type of metal-core PCBs with thermal conductivity ranging from 1W/m.K up to 398W/m.K. The heat transfer is even better than aluminum, and it can handle higher currents and heat dissipation needs. However, its material cost and manufacturing difficulty are also higher.
Aluminum LED PCB
Aluminum substrate are made by laminating aluminum metal with other materials. The advantages of this type of substrate are clear. Aluminum’s superior heat transfer properties, with thermal conductivity typically in the 1W/m.K to 8W/m.K range, allow it to dissipate heat efficiently, supporting higher LED densities and longer runtimes. Its durability and impact resistance are also superior to FR-4, allowing it to withstand the stresses of manufacturing and use. Aluminum is also environmentally recyclable, non-toxic, dimensionally stable and resistant to deformation at high temperatures. This makes it particularly suitable for LED applications that require efficient thermal management. As the most common type of LED PCB, we can take a deeper look at aluminum LED PCB.
Aluminum LED Circuit Board Construction
The Aluminum LED PCB consists of three main layers: Base Layer, Insulation Layer, and Circuit Layer, each of which serves a specific purpose:
Base Layer
The foundation layer consists of aluminum alloy. Acts as the framework, for the entire PCB board to offer stable structural support to the additional layers while also aiding in thermal conductivity to some extent.
Insulating Layer
This layer is made of a ceramic polymer material and serves as an insulator and heat sink. It absorbs the heat generated by the passage of electric current and conducts it to the aluminum layer for dispersion.
Circuit Layer
The circuit layer consists of copper conductors that are wired according to the specific circuit design to ensure the connection of electronic components.
Types of Aluminum LED PCB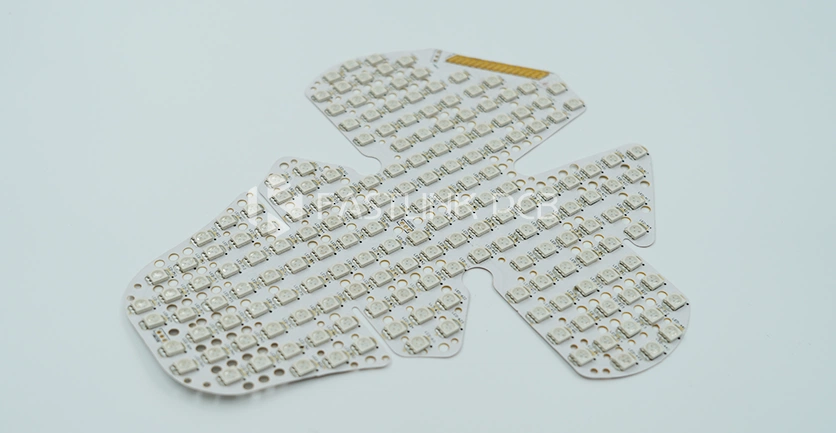
Flexible Aluminum PCB
Composed of an aluminum substrate, polyimide resin, and ceramic filler, flexible aluminum PCBs have good flexibility and insulation properties while retaining the high thermal conductivity of aluminum. These aluminum LED PCB can be bent for mounting, eliminating the need for connectors and cables for applications requiring complex shaped connections. It is important to note that they are designed for one-time bending fixing rather than repeated dynamic bending.
Hybrid Aluminum PCBs
Hybrid aluminum PCBs combine an aluminum-based material with a non-thermally conductive substrate such as FR-4. With this design, manufacturing costs can be reduced and the rigidity of the board enhanced. Although slightly less thermally conductive than pure aluminum PCB, they still provide reliable heat dissipation, balancing performance and cost.
Multilayer Aluminum PCB
These aluminum LED circuit board consist of two or more layer of thermally conductive media to meet the high performance need of complex circuits. The multi-layer design provide additional functionality. However, a multi-layer design can also result in a longer heat conduction path, which can affect its thermal conductivity. By incorporating thermal vias, thick copper insert, thermal management coating, etc. into the PCB layout design, we can meet both functional complexity and good thermal conductivity.
LED PCB Design Considerations
The quality of an LED printed circuit board is highly dependent on the average lifetime of the LEDs used in it. Below are some of the design approaches used to improve the quality of LED printed circuit boards:
1.Thermal management optimization
- Use materials with high thermal conductivity, such as aluminum or metal substrates, to conduct heat efficiently.
- Disperse heat through large copper-filled areas and thermal pad to avoid heat concentration.
- Use heat via in multilayer boards to quickly direct heat to heat dissipation areas.
- For high power circuits, add heat sinks or other cooling measures to ensure that temperatures are within safe limits.
2.Power supply and control circuit design
- Ensure that the power supply and driver circuits accurately match the voltage and current requirement of the LED.
- Add surge protection and overcurrent protection devices, such as fuses or decoupling capacitor, to ensure circuit safety.
- Place the driver circuit as close as possible to the LED pad to minimize voltage loss and energy loss.
- Use reliable grounding technique and reasonable alignment widths to meet current requirements.
- Incorporate test point in the design to facilitate subsequent inspection and maintenance.
3.Layout and wiring strategy
- Prioritize the layout of power supply and grounding lines to ensure stable power supply before laying out the signal.
- Separate the power supply and signal alignment to avoid electromagnetic interference.
- Avoid short cuts as much as possible to improve signal integrity.
- For SMD LED PCBs, place chips together as much as possible to optimize automated assembly efficiency.
4.Multiplexing and Matrixing Technology
- Simplify circuit complexity by controlling multiple LEDs in a matrix using a matrixed design for a variety of lighting and image display solutions.
- Add PWM signals to each row to adjust the overall brightness of the matrix.
- Pay attention to the use of specialized LED driver ICs to manage the control of columns and rows for efficient operation.
5.Line Scan Technology
- Use row scanning technology to divide the display into groups of equal parts (e.g., a 16-row, 32-column matrix is divided into 4 groups).
- Each row of each group is lit sequentially according to the row order, and control of all LEDs is realized using fast switching.
- Fast switching using driver ICs and MOSFETs ensures efficient control with low power consumption.
- The line scan method is particularly suitable for large LED display boards, effectively reducing power consumption and extending the life of each LED.
LED Chip Assembly Technology
SMD and COB are two common LED chip assembly technologies, each with its own characteristics in terms of design, performance and application.
SMD LED
SMD LED are mounted directly on the PCB by means of surface mount technology SMT. SMD LEDs are extremely common in the LED lighting market due to their cost-effectiveness and universal applicability. During the production process, SMD LEDs are automatically picked up and placed on the LED PCB, where they are reflow soldered to form a stable electronic connection. Ultimately, by bonding to the housing, these PCBAs (assembled circuit boards) become full-fledged SMD LED lamps.
SMD technology involve soldering single or multiple LED chip directly to the surface of a circuit board. SMD LED are typically small in size, making them suitable for application that require a compact design, such as LED strip, display and backlighting. However SMD LED are more complex in term of thermal management, especially when multiple LED are densely arranged.
COB LED
COB LED PCB is an integrated packaging technology that package multiple LED chip directly onto a single substrate, eliminating the need for surface mount and reflow soldering. This design provides higher optical density and uniform light output while effectively reducing circuit complexity. Because the chips are densely packaged together, COB LED also outperform SMD in term of heat dissipation. compared to SMD, COB LED are better suited for application that require high brightness and wider illumination, but their color selection is usually less flexible than SMD and their initial cost is higher.
Case Study of Assembly Defects in LED PCB
During the design and assembly of LED PCB, some common problem may be encountered, such as LED not bright, serious color difference or premature light decay. Below are a few specific cases and solution:
1.LED Does Not Light Up (Due to Improper Wiring)
- Problem: The LED PCB of a collocation board is normal in electrical and AOI tests, but some LEDs cannot light up after board splitting. This is usually because the direction of the pads is not perpendicular to the stretching direction of the PCB, resulting in the mechanical stress during depaneling pulling off the gold wires inside the LEDs, leading to an open circuit.
- Solution: In PCB design, especially for aluminum LED PCBs with V-cut depaneling, keep the direction of LED pads perpendicular to the stretching direction of the PCB to reduce the impact of stress during depaneling.
2.Color Difference Before LED Assembly
- Problem: If the LED package has been opened for a period of time, moisture has been absorbed inside the LED chip, and the LED chip has not been baked before assembly, the evaporation of moisture during reflow soldering will trigger the cracking of the internal adhesive layer, resulting in a change in the light path, yellowish or other abnormal color difference.
- Solution: When storing LED, use sealed moisture-proof packaging with a humidity indicator card. For unpacked or damp LED, bake them at 70°C for 24 hours before reassembling them.
3.Flexible LED Strip Failure
- Problem: After soldering a flexible LED circuit board with low-temperature solder paste due to the brittleness of the paste, when the LED PCB is bent the solder joints tend to come off resulting in an open circuit.
- Solution: Select the solder paste that is suitable for the application of the product, and make sure that its viscosity, wettability and melting point can be adapted to the characteristics of the flexible LED PCB.
4.Premature Light Degradation Due to Poor Heat Dissipation
- Problem: The brightness of the LED light decrease after operating for a period of time. This is because the LED cannot dissipate heat effectively during operation, and the continuous high temperature will accelerate the degradation of phosphor yellowing of encapsulation adhesive, and reduction of luminous efficiency of the chip which will ultimately lead to a rapid decline in brightness.
- Solution: Optimize the thermal management design of the PCB, including choosing a substrate with high thermal conductivity (e.g. aluminum or copper substrate), sufficient copper thickness, and a reasonable heat transfer area. You can also seek thermal management support from a team of professionals.
Final Thoughts
With a deeper understanding of LED PCB, it is easy to realize the importance of the LED assembly process, which is the core to ensure the performance and lifetime of the final product and therefore also require more practical experience to deal with various potential problem. Please feel free to discuss with us if you encounter challenge in your project or need more advice. We are willing to share our experience and help you find the best solution.