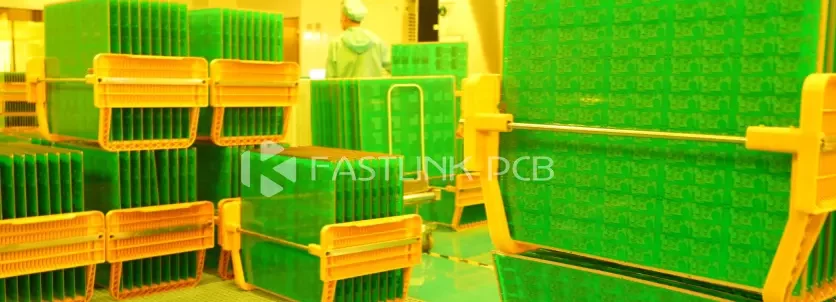
- On August 18, 2024
- In blog
Comments Off on Why PCBs Are Required to Have RoHS Certification?
Why PCBs Are Required to Have RoHS Certification?
The rise in the manufacture and utilization of electronic devices like smartphones, laptops and home gadgets has resulted in a surge in waste. From usage, collection, processing to disposal, toxic elements such as lead, mercury and cadmium may be released, presenting environmental and health hazards. In response to these issues, the European Union introduced the RoHS Directive to restrict the presence of hazardous substances in electrical and electronic devices giving rise to the creation of RoHS compliant PCB.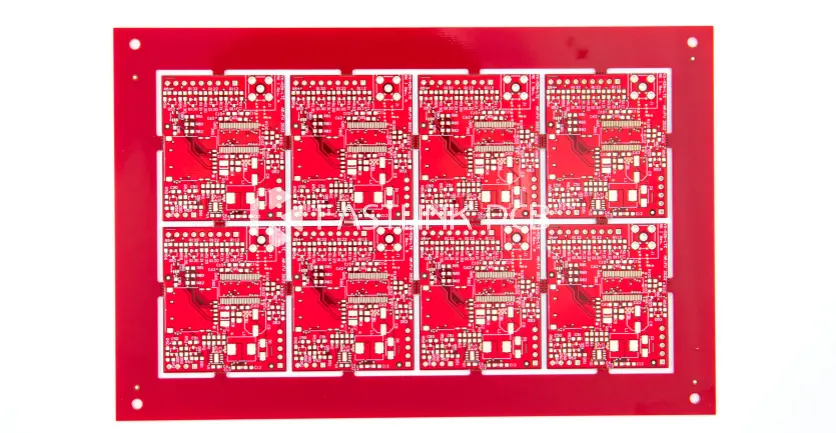
While RoHS was first introduced in Europe, manufacturers often have global supply chains and find it more efficient to adopt RoHS compliance across all their products, regardless of final destination market.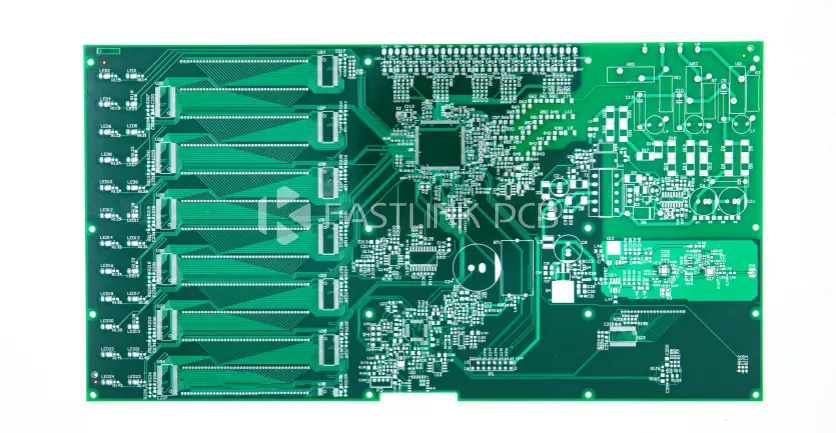
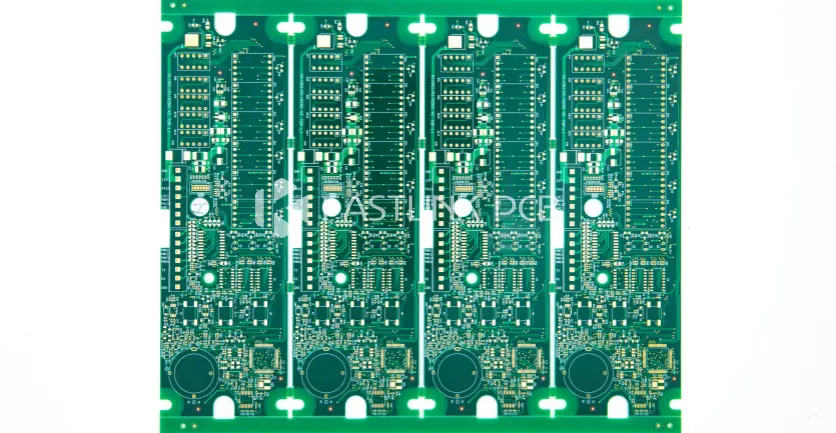
More than a decade, Fastlink has focused on developing environmentally friendly RoHS PCBs manufacturing techniques. Our dedication to environmental consciousness motivates our PCB adhere to the strictest regulatory requirements.
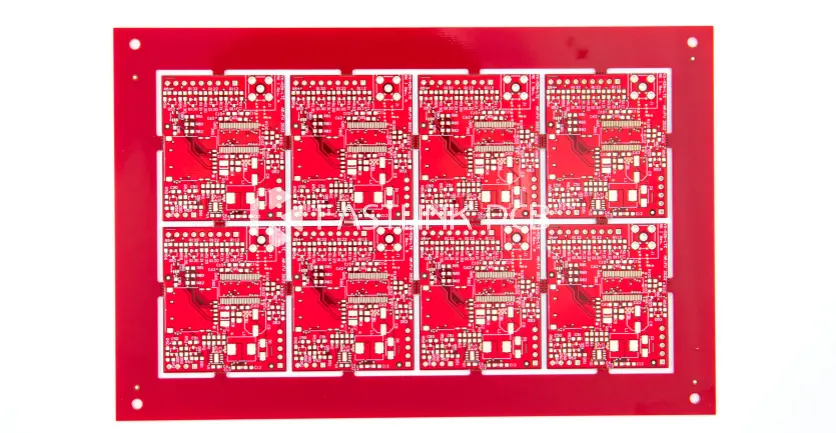
What Is a RoHS Compliant PCB?
A RoHS compliant PCB, hereinafter referred to as RoHS PCB, standing for Restriction of Hazardous Substances PCB, is a type of printed circuit board that comply with the RoHS directive. This means that it is produced without the use of hazardous substances prohibited by the RoHS directive, guaranteeing the final product meets RoHS directive.What Is RoHS?
Aiming to reduce the impact of electronic waste on human health and the environment, the RoHS Directive, initially established by the European Union, beginning with RoHS 1 (2002/95/EC), which was adopted in 2003 and implemented in 2006 mandates that all electronic and electrical devices sold in EU member nations comply with RoHS criterias, restricting the use of 6 hazardous substances. RoHS 2 (2011/65/EU), adopted in 2011, expanded the scope of the regulation and introduced requirements for compliance documentation. RoHS 3 (2015/863/EU), adopted in 2015, in effect since 2019, added 4 more substances to the restricted list.SI.NO | Restriction of Hazardous Substances (RoHS) List | Permissible Value in terms of PPM (parts per million) |
1 | Lead (Pb) | <1000 PPM |
2 | Mercury (Hg) | <1000 PPM |
3 | Cadmium (Cd) | <1000 PPM |
4 | Hexavalent chromium (Cr6+) | <1000 PPM |
5 | Polybrominated-biphenyls (PBB) | <1000 PPM |
6 | Polybrominated-diphenyl ether (PBDE) | <1000 PPM |
7 | Bis(2-ethylhexyl)-phthalate (DEHP) | <1000 PPM |
8 | Butyl benzyl phthalate (BBP) | <1000 PPM |
9 | Dibutyl phthalate (DBP) | <1000 PPM |
10 | Di-isobutyl phthalate (DIBP) | <1000 PPM |
Why You Need RoHS PCBs?
RoHS PCB is essential for the environment, health considerations, the market access and the consumers trust.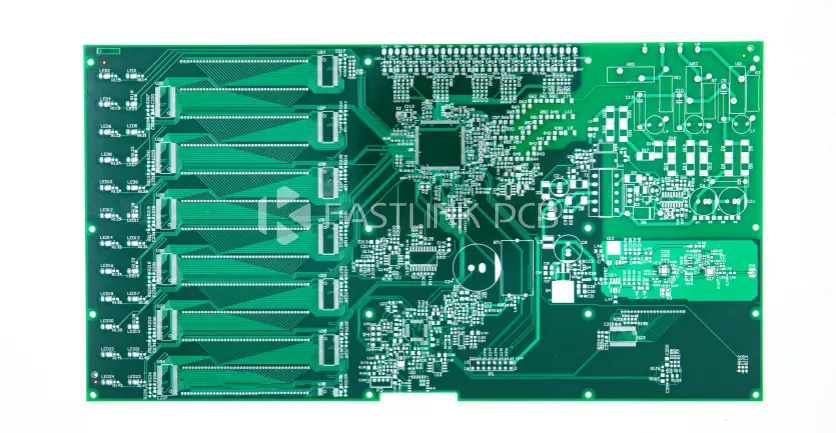
Environmental Benefits
RoHS PCBs offer environmental benefits by eliminating hazardous substances from the production, usage, disposal and recycle, which reduce environmental pollution, contribute to waste reduction and a greener electronics industry.Health Benefits
RoHS PCBs provide health advantages benefiting both the employees engaged in production and the end users.Market access
Because RoHS is mandatory in many regions, RoHS PCB enables seamless integration into the global supply chain, it is essential for global market access.Customers Trust
Adherence to RoHS regulations through the use of RoHS PCB can demonstrate company’s commitment to sustainability and corporate social responsibility, the commitment to environmental and health-conscious practices can resonate with customers, fostering a sense of trust and goodwill towards the brand.Materials Used in RoHS PCBs
Materials used in RoHS PCB must ensure compliance with the RoHS.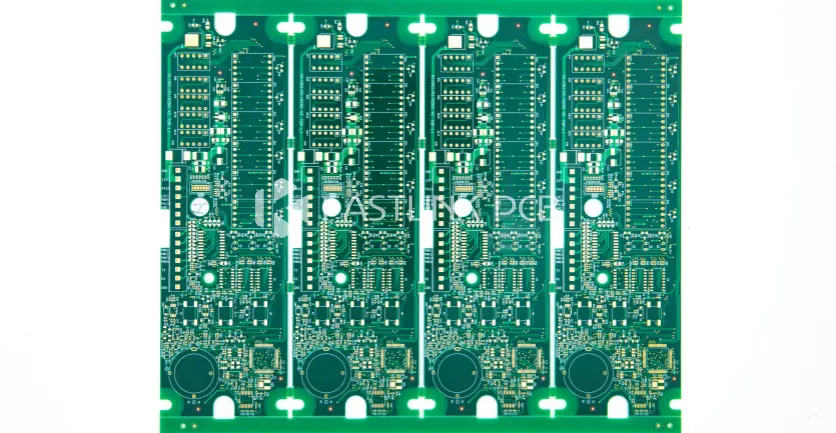
Base Laminates
Fiberglass reinforcement laminates like FR-4, BT resin or ceramic substrates with high Tg could be used, as long as they comply RoHS regulations.Copper Foiling
Lead free copper is used to create the pathways on the printed circuit board, lead free copper means that the copper doesn’t have any extra lead or has a very minimal amount of lead usually less than 0.1%.Solder Mask and Legend
Many epoxy-based solder masks are water-soluble alternatives and RoHS compliant. Similarly, most ink formulations for PCB legends adhere to RoHS restrictions.Solder
Lead free solders like tin-silver-copper (SAC), tin-lead-silver (SnPbAg), tin-copper (SnCu), or tin-zinc (SnZn) are commonly employed.Surface Finishes
RoHS-compliant surface finishes are free of lead, like immersion tin, immersion silver, immersion gold (ENIG), or organic solderability preservatives (OSP), etc., are employed to protect the copper traces and facilitate soldering.Flame Retardants
To meet the requirements of the RoHS directive, halogen-free flame retardants are employed that do not contain PBB and PBDE banned under RoHS directive.Challenges of Manufacturing RoHS PCB
The RoHS directive prohibits the use of lead, mandating lead free soldering in the production of RoHS PCBs. It necessitates replacing lead-based solder with lead-free alternatives like tin-silver-copper (SAC) alloys and adjusting the soldering process accordingly. Lead-free solders have higher melting points and different wetting and flow properties, requiring modifications to parameters such as reflow profiles and higher temperature settings.Difference Between Lead Free PCB and RoHS PCB
A lead-free PCB is a printed circuit board that does not contain lead, a toxic metal in its solder joints. The primary focus is on the solder, which is replaced with lead-free alloys such as tin-silver-copper (SAC), tin-copper (SnCu), or tin-zinc (SnZn). RoHS directive limits the use of several hazardous substances, including lead (Pb). So all lead free PCBs are RoHS PCBs, as lead is one of the restricted substances under RoHS.Typically, lead-free solders are composed of:- Tin (Sn): The primary element, providing good wetting properties.
- Copper (Cu): Improves mechanical strength and reduces oxidation.
- Silver (Ag): Enhances solderability and reduces melting point.
- Other elements: Sometimes, elements like bismuth (Bi) or indium (In) are added for specific properties.
Why Choose Fastlink?

RoHS Compliant Surface Finishes
Fastlink provides RoHS and lead-free circuit boards, come with a variety of surface finishes to choose from.Surface Finishes | Shelf Life | Co-Planarity |
ENIG/Immersion Gold | 12+ Months | Yes |
Immersion Silver | 6-12 Months | Yes |
Immersion Tin | 3-6 Months | Yes |
Lead Free HASL | 12+ Months | Moderate |
OSP | 6-12 Months | Yes |
RoHS Certificated
Since 2010, we have held RoHS certification demonstrating our commitment to following RoHS PCB standards, this commitment reflects our focus on sustainability and the human health it ensures.Lead Free Process
We employ cutting edge manufacturing techniques in our RoHS compliant PCBs to meet environmental and quality criteria. Our PCBs adhere to RoHS regulations, do not contain harmful substances like lead during production, promoting a safer environment.Selected Raw Materials
We are meticulous in our selection of raw materials including base laminates, solder alloys, surface finishes, etc that adhere to RoHS compliance standards. When you opt for Fastlink you’re selecting a partner committed to quality and eco conscious methods throughout the PCB production process.Contact Us
- Aluminum PCB
- Flexible PCB
- Multilayer PCB
- Rogers PCB
- Heavy Copper PCB
- Ceramic PCB
- PCB Prototype
- Rigid PCB
- Rigid Flex PCB
- High Tg PCB
- HDI PCB
- High Frequency PCB
- High Speed PCB
PCB Assembly
Automated Optical Inspection (AOI)
Through Hole PCB Assembly
Flex PCB Assembly
Prototype PCB Assembly
PCB Box Build Assembly
Electronic Assembly Services
Low Volume PCB Assembly
PCBA Components Assembly
Mixed PCB Assembly
IC Coding Programming
Consignment PCB Assembly
Electronic Manufacturing Service
高速PCB